علی رغم بهتر بودن نسبی کیفیت نهایی رابرلاینینگ گرم، محدودیتهایی وجود دارد که باعث میشود سهم عمدهای از رابرلاینینگ ها به روش سرد اجرا شود که برخی از آنها عبارتند از:
1-بزرگی قطعات و مخازن به نحوی که نتوان آنها را داخل اتوکلاو قرار داد، البته فرمولاسیون بعضی از لاستیکها به نحوی طراحی می شوند که در فشار و دمای کم (مثلاً فشار حدود 1.5 Bar gage و دمای 120 درجهی سانتیگراد ) قابلیت ولکانیزاسیون داشته باشند که در آنصورت می توان با تعبیهی درپوشهای مناسب برای ورودی و خروجی و منهول های مخزن، خود مخزن را به یک اتوکلاو تبدیل نمود.
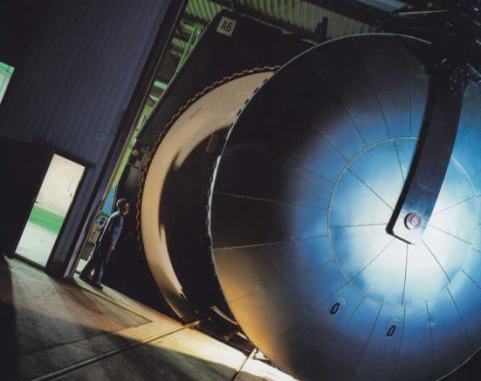
اتوکلاو غول پیکر جهت ولکانیزاسیون رابرلاینینگ مخازن و قطعات بزرگ در کارگاه
2- مدت زمان محدود نگهداری ورقهای لاستیک خام به دلیل وجود مواد پخت در فرمولاسیون آنها که باعث میشود پس از تولید نحوهی نگهداری محصول در دمای محیط یا سردخانه بین 2 تا 6 ماه باشد، که باتوجه به زمان حمل و ترخیص برای کالاهای وارداتی باعث بحرانی شدن زمان انقضا مصرف می شود.
3- بالاتر بودن هزینهی حمل لاستیک خام در کانتینرهای یخچالدار و نگهداری در سردخانه.
4- طولانی تر بودن مدت زمان نصب لاستیک به دلیل اضافه شدن عملیات پخت و کنترلهای کیفی مضاعف پس از کیورینگ.
5 -بالاتر بودن هزینهی نصب لاستیک به روش گرم به دلیل طولانی تر بودن مدت عملیات نصب و نیاز به امکانات کارگاهی بیشتر نظیر، دیگ بخار و کمپرسور باد.
6- ریسک کیور نشدن یا اورکیور شدن قسمتهایی از رابر پس از انجام عملیات پخت به دلیل ضعف یا محدودیت تجهیزات کنترل پخت در سایت.
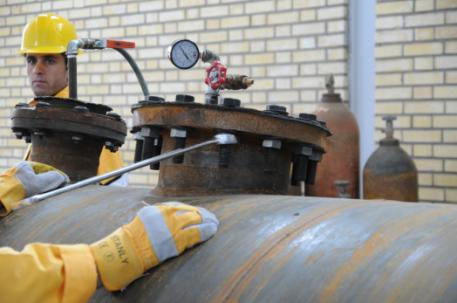
عملیات پخت لاستیک در سایت تحت فشار و حرارت بخار با تبدیل کردن خود مخزن به اتوکلاو